Introduction
In the fast-paced world of food packaging, where efficiency, convenience and environmental sustainability come together, PS food container forming machines are rapidly changing the industry. These cutting-edge machines play a vital role in producing the popular PS food containers that are commonly seen in our daily lives.
In this blog, we take an in-depth look at the technology behind the PS food container forming machine and its significant impact on food packaging quality and the environment. By exploring every aspect of these machines, we reveal how they contribute to the seamless production of food containers, maintain hygiene standards and encourage sustainable practices. So, let’s dive into the fascinating world of PS food container forming machines and see first-hand their revolutionary potential.
1. Understand PS food container forming machine:
PS food container forming machines are state-of-the-art equipment designed to mass-produce food containers ranging from cups and bowls to trays and clam shells using polystyrene (PS) as the main material. These machines are equipped with cutting-edge technology, automation features, and innovative features that simplify the container forming process.
When starting production, the raw material PS pellets are loaded into the hopper, then heated and melted. The molten PS is then injected into a special mold according to the desired container shape. The mold is then cooled and opened, allowing the formed container to automatically eject, ready for further processing and packaging.
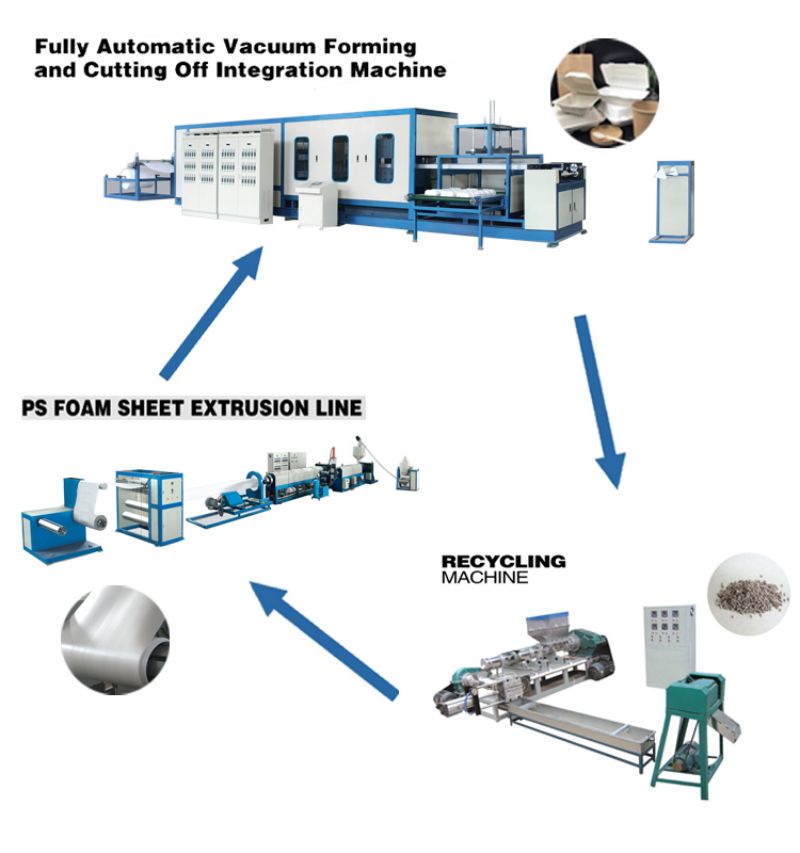
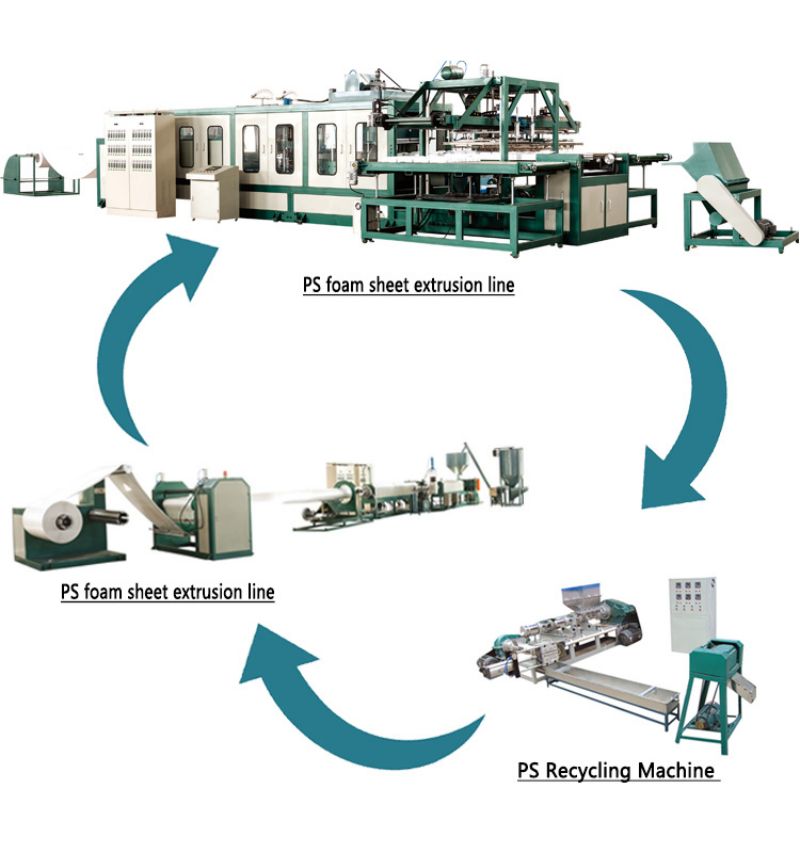
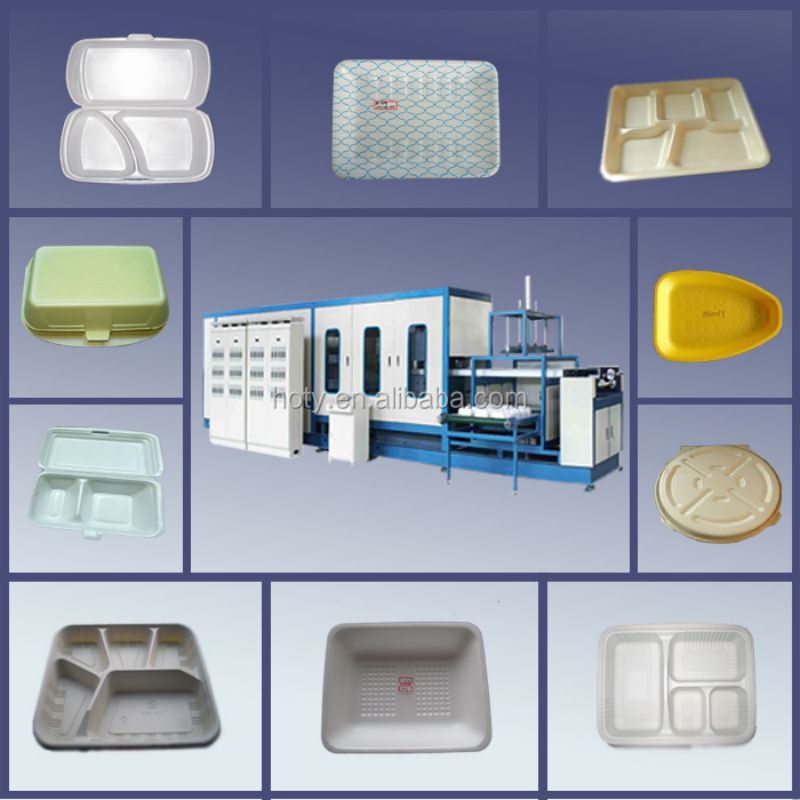
2. Improve efficiency and hygiene :
PS food container forming machines offer unparalleled efficiency and hygiene in food packaging. Their automated nature eliminates the need for excessive human intervention, reducing the risk of contamination while maintaining stable productivity. These machines are capable of mass-producing food containers at impressive speeds, increasing productivity and meeting the growing needs of the market.
In addition, PS food container forming machines can precisely control container specifications, ensuring consistency in shape, size and quality. Increased accuracy minimizes the occurrence of container defects or malformations, reduces waste and optimizes material costs.
To further enhance hygiene levels, these machines are equipped with advanced sterilization systems that prevent bacterial growth and contamination. These systems use ultraviolet (UV) or other disinfection technology to ensure the highest levels of cleanliness and food safety.
Post time: Oct-19-2023